News & Insights
Modular Construction: Building Woodfibre LNG One Piece at a Time
Mar 27, 2025
Located along the southwest coast of British Columbia, Woodfibre LNG is set to become the world’s first net-zero LNG export facility. While construction on-site began in September 2023, the Project has adopted a modular construction approach to enhance efficiency and meet its construction timeline. As part of this strategy, the fabrication of key LNG modules is currently underway overseas, where 19 specialized modules are being constructed. This method has been shown to improve timelines, increase efficiency, and enhance quality control in large-scale projects, all while minimizing environmental impact. In this article, we’ll explore how this approach is helping Woodfibre LNG achieve its construction goals, reduce its environmental footprint, and position the facility to produce approximately 2.1 million tonnes of LNG annually once operational.
What is Modular Construction?
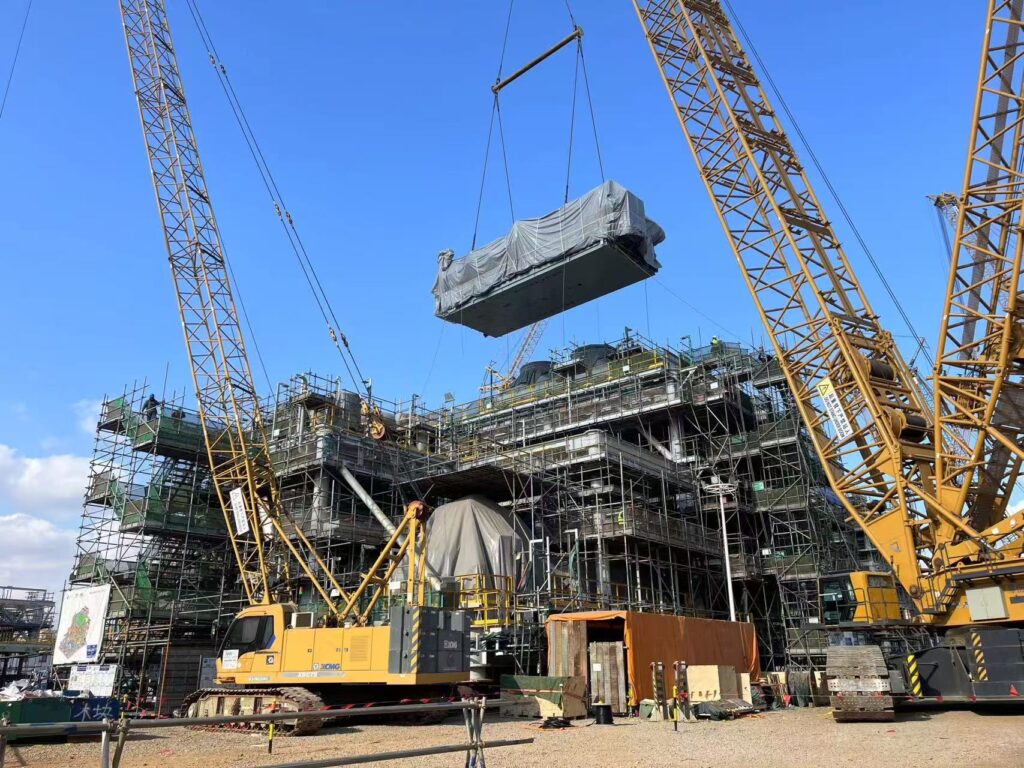
Modular construction is a method of building large-scale industrial projects by fabricating major components—or modules—off-site in a controlled environment. These modules are transported to the final project location for hook-up instead of being built on-site or “stick-built”. This method allows for improved project cost efficiency, better quality control, and faster project completion versus on-site construction.
At its core, modular construction involves breaking down a facility into pre-assembled units (PAU) or modules that house key systems and equipment. These modules can range in size from small process skids to massive multi-story structures containing complex piping, electrical systems, and heavy industrial machinery. By assembling these components in specialized fabrication yards, modular construction enhances productivity and off-site pre-commissioning reliability, while minimizing environmental and logistical challenges on-site.
For the Woodfibre LNG project, modular construction is a critical part of delivering the world’s first net zero LNG export facility. The majority of the plant’s key components are being built off-site, allowing for seamless integration of pre-tested and ready for hook-up modules once they arrive at the project’s location in Squamish, British Columbia.
Why Are We Using Modular Construction?
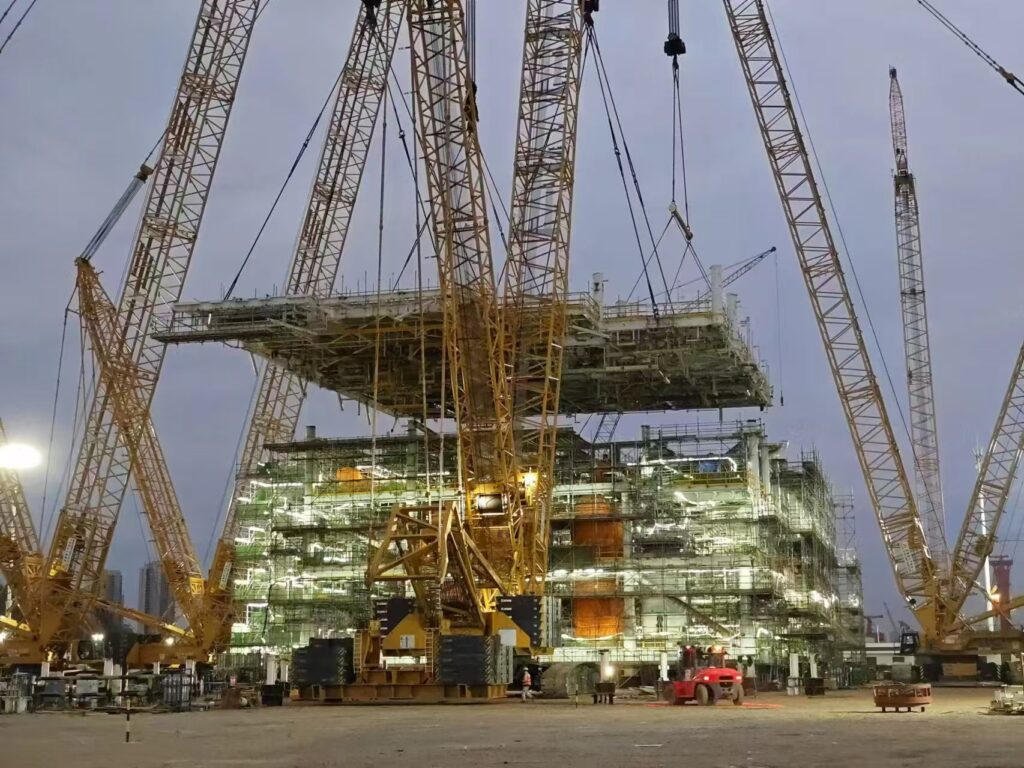
Woodfibre LNG has adopted modular construction for several key reasons, all of which contribute to the safe and efficient construction of the Project.
1. Improved Quality Control
Manufacturing modules in a controlled facility such as the Module Assembly Shop allows 24/7 all-weather operations that enhance quality assurance. Every component is assembled under consistent conditions at specialized facilities that produce repeatable high quality work, with rigorous testing and inspections that ensure the modules meet high engineering and safety standards.
2. Increased Efficiency and Speed
One of the greatest advantages of modular construction is its ability to reduce overall project timelines and predictable outcomes with careful quality management. Since module fabrication happens simultaneously on multiple fronts while site preparation and foundation work are completed in Squamish, construction activities and resources are streamlined. This approach reduces the time required for on-site assembly, allowing the facility to be built faster than if all work had to take place on location.
3. Enhanced Worker Safety
Off-site fabrication reduces the number of construction personnel needed at the project site, decreasing the risk of injuries associated with working in remote or extreme environmental conditions. Fabrication yards are equipped with state-of-the-art tools, lifting equipment and infrastructure to ensure safe and efficient module assembly, mitigating the hazards of working at height. The controlled work environment inside the Module Assembly Workshop also protects against unpredictable weather conditions which reduces downtime.
In addition, using a facility and staff experienced in building large process modules increases the likelihood of achieving higher quality, meeting safety standards, and delivering on time to meet the project’s first LNG export deadline.
4. Minimizing Our Site Footprint
One of our core priorities at Woodfibre LNG is to minimize impacts whenever possible. By shifting a significant portion of construction off-site, the physical footprint of on-site work is smaller. This means less habitat disturbance from site clearing, less congestion of equipment and people on-site, and fewer boat trips transporting equipment and materials to and from site.
5. Cost-Effectiveness
Off-site construction often results in lower costs by enhancing productivity, streamlining labour resources using automated assembly processes (such as automatic welding), optimizing material use and wastage and minimizing expensive on-site downtime and schedule delays. With materials procured and assembled in a single location before transportation, there is less risk of unexpected cost overruns due to weather disruptions or workforce shortages at the project site.
Where is Modular Construction Happening?
Fabrication is underway at the QMW McDermott Fabrication Yard, one of the world’s leading modular construction facilities specializing in large-scale modular projects. Nineteen specialized LNG modules and racks are taking shape here, some weighing in excess of 10,000 metric tonnes. This yard is known for its advanced manufacturing techniques, precision engineering and experience in delivering high-quality modules for LNG projects globally.
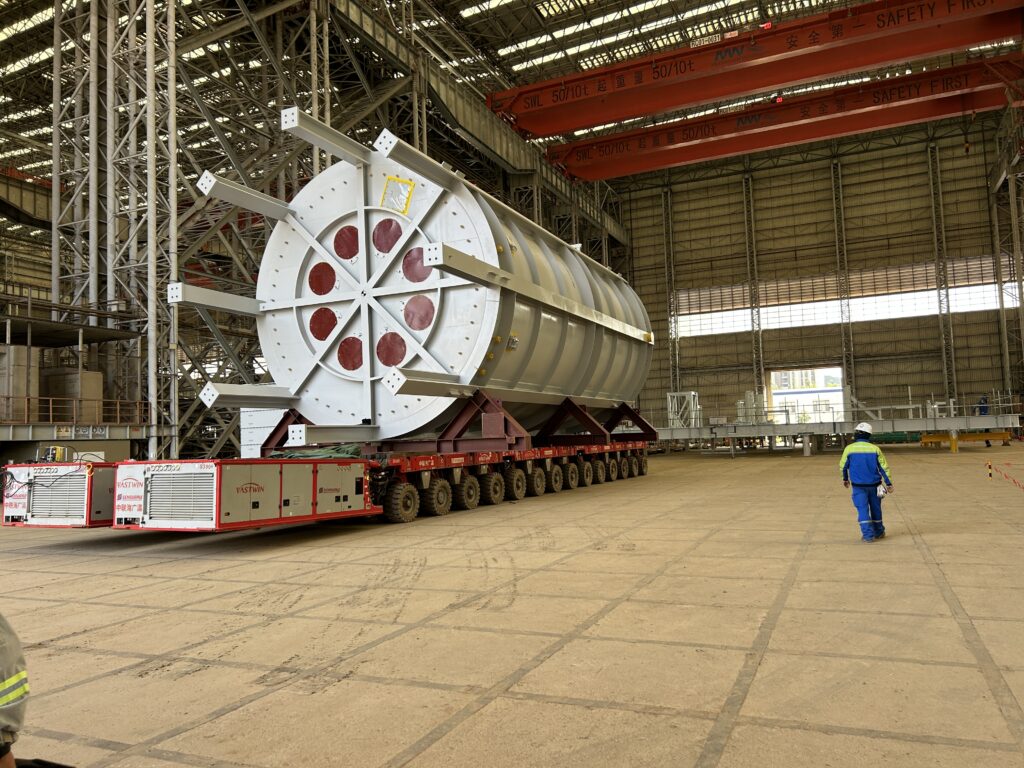
Located in Qingdao, China, the facility is equipped with world-class infrastructure, including:
- An approximately 26,000 sq ft all-weather module assembly shop, operating 24/7
- Heavy-lift cranes capable of handling massive modular components and deck stacking activities
- Dedicated testing and inspection facilities to ensure the modules meet the highest safety and performance standards.
- Streamlined production lines designed specifically for complex LNG and energy-related modules.
The fabrication yard operates under stringent international quality control processes, ensuring that each module adheres to strict engineering specifications and build standards. Once completed and tested, these modules are prepared for shipment, carefully transported via specialized vessels, and delivered to Squamish, where they will be hooked up together.
The Journey from Fabrication Yard to Squamish
Once completed, the modules embark on a meticulously planned journey from China to Canada. Given their immense size and weight, transporting these modules is a significant engineering feat in itself.
Here’s how the process unfolds:
- Inspection & Certification: Each module undergoes rigorous quality checks before being cleared for weighing and then transport.
- Specialized Shipping: Modules are loaded onto heavy-lift cargo vessels, designed to transport oversized industrial components which are sea fastened to the vessel prior to sail away
- Marine Offloading: Upon arrival at the Woodfibre LNG site, the modules are carefully offloaded at the Marine Offloading Facility (MOF), a dedicated structure built to handle large shipments
- Final Hook-Up: Once on land, the modules are transported to their designated locations within the Woodfibre LNG site and set onto their respective foundations, where final site integration work takes place.
Looking Ahead
The first modules, a series of pipe rack modules that connect the liquefaction and loading facilities, are scheduled to arrive this summer. This marks the beginning of a series of module deliveries that will continue throughout the remainder of 2025 and into early 2026.
Modular construction is an integral part of how Woodfibre LNG is being built safely and efficiently. By leveraging off-site fabrication at the QMW McDermott yard, the project is upholding the highest standards of quality while expediting the construction timeline and ensuring a minimal footprint at the Project site.