About LNG
About Liquified Natural Gas
Liquified Natural Gas (LNG) is natural gas that has been cooled down -162°C, at which point it becomes liquid.
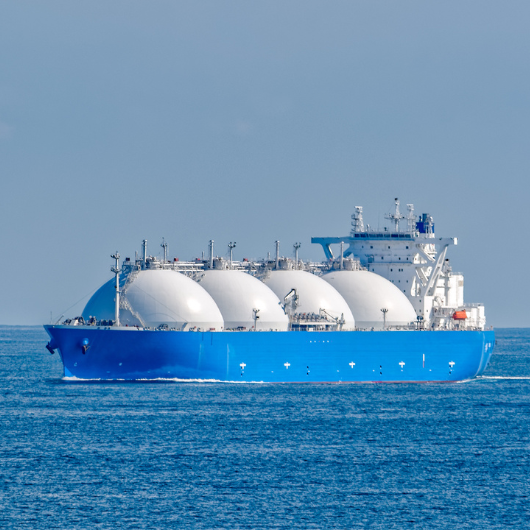
In its liquid state, LNG takes up approximately 1/600th the volume of natural gas and can be more easily stored or transported in a non-pressurized state. It is colorless, non-toxic, and non-corrosive.
The majority of LNG produced for export in Canada will serve demand in Asian markets.
How the Woodfibre LNG Facility Works
The Woodfibre LNG facility is a natural gas liquefaction and export facility, designed to produce 2.1 million tonnes of LNG per year for overseas markets. It has been designed to be among the lowest greenhouse gas emitting LNG facilities in the world and, using nature-based offsets to counter hard-to-abate emissions, will be the world’s first net zero LNG facility.
The project site itself is just a single square kilometre and the facility itself has been designed to have as minimal impact on the landscape as possible.
An LNG export facility is a specialized and complex piece of infrastructure designed to liquefy natural gas for more efficient transport and long-distance export.
Liquefaction Process
Gas Intake
The process begins with the intake of natural gas from a nearby pipeline. Woodfibre LNG will receive its gas through the Eagle Mountain – Woodfibre Gas Pipeline Project, an extension to the FortisBC pipeline system being built by FortisBC.
Pre-Treatment
Before liquefaction can occur, the natural gas undergoes pre-treatment to remove any impurities to ensure it meets the quality standards required for liquefaction. As the gas being received from FortisBC is already of pipeline quality and ready for use, pre-treatment at Woodfibre will be minimal.
Liquefaction
This is the heart of the facility. The natural gas is cooled down to extremely low temperatures using a refrigeration process. This cooling causes the gas to undergo a phase change from a gaseous state to a liquid state when the temperature hits about -162°C. This compression of gas creates energy-dense LNG, shrinking the gas into a form that is more efficiently stored and transported.
Woodfibre LNG is a single train facility, meaning it has a single liquefaction module. This smaller arrangement better fits the small footprint of the Woodfibre LNG site.
Woodfibre LNG was the first LNG export facility in Canada approved to use electric compressors in its liquefaction module instead of gas-powered turbines. Powered by renewable hydroelectricity, these electric drive compressors help Woodfibre LNG achieve among the lowest emissions profile in the industry at just 0.04 tonnes of CO2e per tonne of LNG.
Storage
The newly formed LNG is stored in insulated tanks to keep it at the low temperatures required to remain in a liquid state. Tanks are double-walled with an insulating vacuum between the walls to minimize heat transfer. Woodfibre LNG will utilize floating storage, using two modified LNG carriers, to reduce the facility’s footprint at site.
Loading
Once the LNG is ready for export, it can be loaded onto specialized LNG carriers, which are ships designed to transport LNG at very low temperatures. Using cryogenic hoses and arms, LNG will be transferred into the carriers. Carriers will arrive approximately every 10 days for loading.
Export
LNG carriers transport the liquefied natural gas to its destination, which is often another country. These carriers are equipped with advanced containment systems to keep the LNG at its cryogenic temperature during transit and are fueled by the LNG they are transporting.
Receiving Terminal
At the destination, a receiving terminal is required to regasify the LNG back into a gaseous state before it can be distributed through pipelines or used for various applications, such as electricity generation or heating.
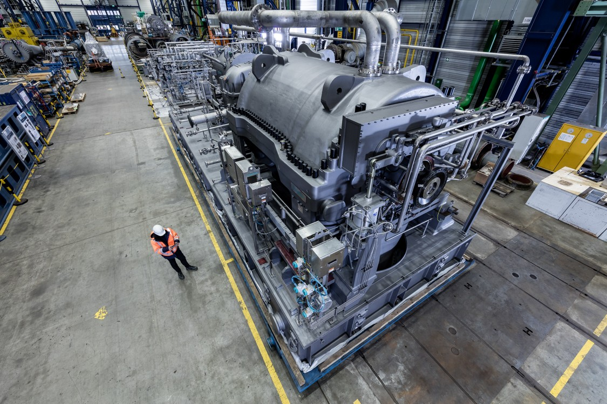
Siemens E-Drive
A distinguishing feature of the Woodfibre LNG facility is the use of electric drive compressors instead of gas-powered ones. Although an industry standard, gas powered drives are the primary source of greenhouse gas emissions (GHG) in LNG facilities worldwide. By utilizing electric drive systems, powered by renewable hydroelectricity from BC Hydro, Woodfibre can further reduce its carbon footprint. Electric drives produce no GHG emissions and are key in meeting our net zero commitment.
Electric drive systems also have a higher efficiency rate compared to internal combustion engines commonly used in gas-powered drive systems. This can result in reduced energy consumption and more precise control of equipment, enabling operators to optimize processes and minimize wastage. This efficiency can lower operational expenses and contribute to the overall sustainability of the facility. Finally, electric drive systems offer operational flexibility and reliability. They can be easily controlled, started, and stopped as needed, providing precise and rapid response to changes in demand. In contrast, gas-powered drive systems may require time-consuming warm-up and cool-down periods, making them less adaptable to fluctuating production requirements. Electric drive systems also tend to require less maintenance, resulting in reduced downtime and increased overall operational reliability.